De Heus opens three brand new factories in Uganda, India and Kenya
In a significant and unprecedented milestone, three new De Heus feed mills are commencing operations in Uganda, India and Kenya — all within a period of just three months. By providing safe, high-quality feed, these facilities will help local farmers improve their business performance and contribute to sustainable food supplies in these countries. This remarkable achievement demonstrates De Heus’ capacity to rapidly scale its impact across multiple geographies, reinforcing its long-term vision for responsible food production.

Inefficiencies in the value chain
Uganda, Kenya and India are all dealing with inefficiencies in their value chains. "In Uganda, fish is a big part of the country's diet," says Stefan van den Bogaard, Group Director Technology & Investments. "Aquaculture is growing, but almost all aquafeed is imported so the price of fish feed is too high. The first step towards a sustainable food supply is domestic production of high-quality aquafeed. That's why we've invested in an aquafeed plant in Njeru, near Jinja, on the north shore of Lake Victoria. By reducing dependence on imported feed, avoiding stock-outs, and providing high-quality extruded aqua feed, we will help lower costs for local farmers and increase their incomes."
Ensuring safe, high-quality animal feed
Kenya relies heavily on imported raw materials, which is one of the key reasons agriculture has become the government's top priority. "They're also concerned about the health of the population," explains Stefan. "That's why the government is very happy to welcome companies like De Heus, who take food safety seriously." The new De Heus factory in Athi River, near Nairobi, is a dedicated animal feed plant and will serve the country's poultry, swine, and ruminant sectors. The situation in India is slightly different to Uganda and Kenya. "We already produce animal feed at various rental factories in India," says Stefan. "With our greenfield project, we have already ceased operations at one of the rental facilities, and will gradually end the remaining ones — underlining our long-term commitment and trust in the Indian market. Our new factory in Rajpura, Punjab, similarly will produce stable, reliable, high-quality feed for ruminants, swine and poultry, which will help farmers improve their performance."
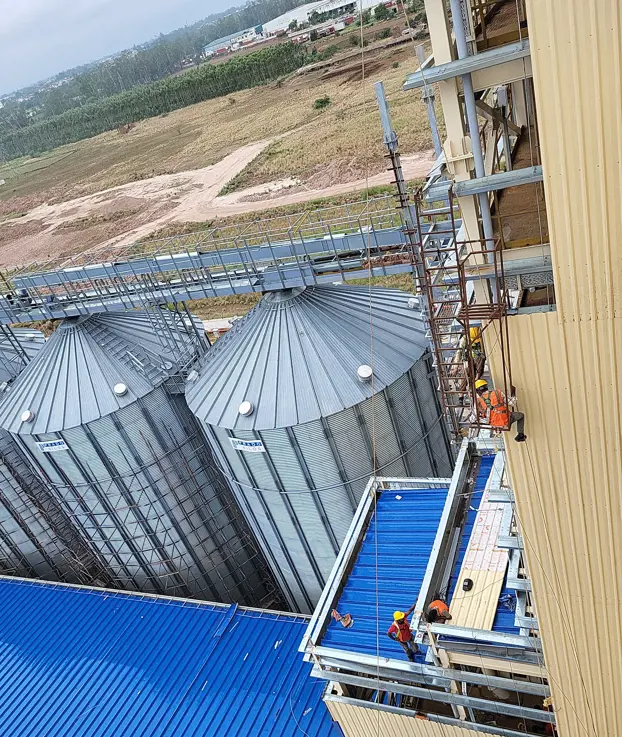
Cutting-edge factories
All three feed mills will be modern facilities using state-of-the-art equipment. "We import equipment to ensure high production efficiency and stable quality," says Stefan. "Our suppliers include several international companies with whom we've built strong relationships through our operations in Europe and Asia." In choosing equipment, quality is always paramount. "In Uganda, for example, we could use horizontal dryers which are generally easier to operate and cheaper," continues Stefan. "But they don't deliver the same superior results as vertical dryers. This is what we learned by experience in other aqua plants.". Moreover, our Group CAPEX team members design the entire production process in-house, giving the company a major competitive advantage across the globe.
Ensuring feed quality and performance
To safeguard feed quality, all three feed mills will also have their own professional laboratory on site. "Quality control is key for us," emphasises Stefan. "It's about both nutrient values and feed safety." In these laboratories, all raw materials and finished products undergo stringent testing to check for contamination and verify nutrient levels. "If we're selling a product with say 25% protein, it's actually in there with a very small variance," says Stefan. "Some of our local competitors conduct far fewer lab tests and some of the smaller ones don't even test at all." As a result, farmers can rely on a stable quality of De Heus feed consistently, which is vital for them for improved animal health and performance.
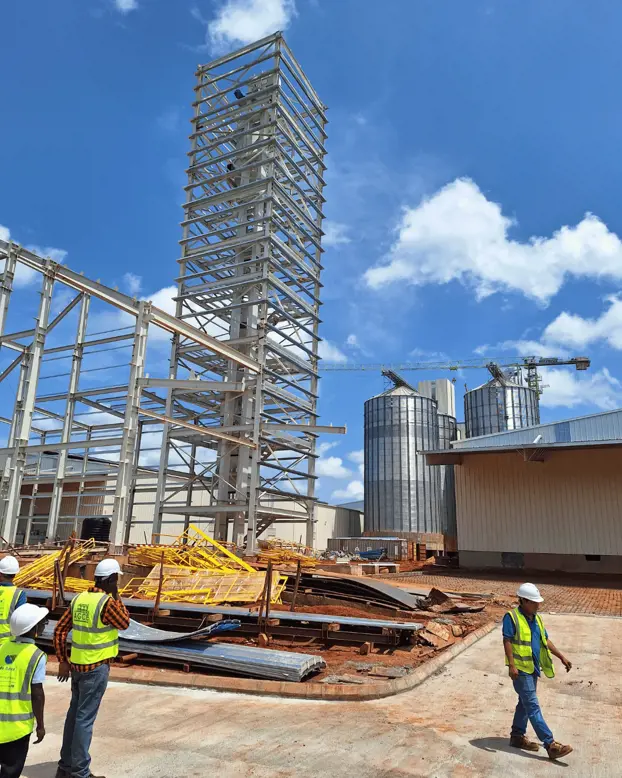
Overcoming construction challenges
Building factories in other countries isn't always smooth sailing though. A substantial part of the construction materials and equipment are imported from Europe and Vietnam. "Importing materials and equipment can be a challenge and time consuming, but we do it for very good reasons" says Stefan. “Due to our strong presence in many countries - and because some of our team members having lived abroad - we have preferred suppliers for automation and installation supervision, which we engaged for several projects. “That’s the huge benefit of our global presence and network.”
The strict standards maintained by De Heus are often a new experience for workers. "Many of the labourers have worked all their lives in construction and aren't used to wearing safety boots, helmets and vests," says Stefan. “We don’t make any compromises regarding safety, so we maintain our global standards at these sites.” Attitudes to quality of workmanship are different too, particularly in terms of finishing. "When I visited our office and lab building in Uganda recently, I saw the finish works are at a high standard and we can be proud of that.”
Quality control is key for us. It’s about both nutrient values and feed safety.
The actual construction is carried out by local contractors and workers, which can present challenges—particularly as attitudes towards construction safety and quality can vary significantly across Uganda, India and Kenya. To ensure high standards and smooth project execution, De Heus assigned experienced project managers and technical specialists to each location. These experts oversee all aspects of engineering, procurement and construction, working closely with local teams and plant managers on site. By maintaining a near-permanent presence in both Uganda and Kenya, De Heus ensures consistent quality control, adherence to safety protocols, and close collaboration throughout the entire construction process—critical factors in the successful delivery of all three projects.
Providing local employment and welfare
As well as providing employment for construction workers, the finished factories will be staffed by local people as well. "Besides that it will also lead to indirect employment, for example for electricians and logistics providers," Stefan says. "In line with De Heus' commitment to thriving employees, we offer them good working conditions and treat them well." For example, the so-called welfare block at our factories have professional air conditioning, showers, changing rooms and a canteen with a professional kitchen area offering daily hot local meals.
A unique achievement
The factories in Uganda and India started testing & commissioning in June and are expected to deliver commercial products in August of this year, followed by the Kenyan factory launching in October. "We have built three new feed mills in relatively new markets, with unfamiliar contractors, in three different countries simultaneously," says Stefan proudly. "That's quite unique and demonstrates what De Heus is capable of as a global organisation."
"We started with nothing, so we've had to do all the permitting, engineering and construction management and now the commissioning," Stefan continues. "Besides Technology, a lot of departments have been involved, such as IT, Nutrition & Formulations and Quality, but also Finance, Legal, Marketing and HR. It's great that as a company we can do this." This cross-company approach will continue once the factories are operational. For Example, production specialists, a former plant manager and some operators from Vietnam and the Netherlands will travel to the feed mills to provide support and trainings. Another example is the cross BU support of Ivory Coast, Ethiopia and Ghana to implement the IT systems in Uganda and Kenya. “It’s a true one-team multiple-county effort —an achievement that combines our global mindset and local responsiveness,” concludes Stefan.